The evolution of Menthol synthesis at Bushy Park
Since successfully synthesizing Menthol for the first time fifty years ago and, subsequently becoming one of the biggest suppliers of this new substance, Symrise has continued to optimize and innovate its processes. The plant in Bushy Park, South Carolina, USA, is an excellent example of Symrise’s continual efforts to improve.
In the serene expanses of Bushy Park, a revolution in the synthesis of L-Menthol has been unfolding over the decades. Established in 1977, the facility in the US state of South Carolina has been at the forefront of chemical engineering, adapting and evolving with technological advancements and to meet market demands. Dr Peter Esser, VP Global Chemical Production, and Jared Klein, ASST VP Chemical Production US, for many years engineer and manager of the Bushy Park Menthol Production discuss the journey of the plant from its inception until today.
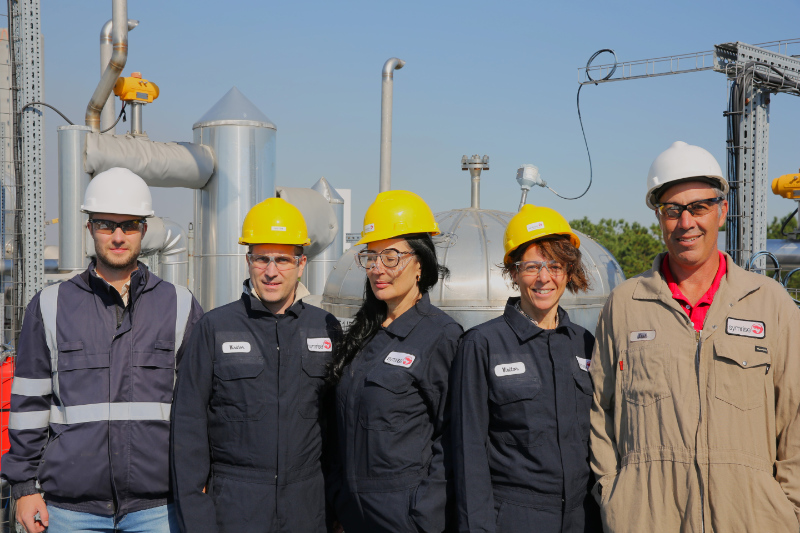
Jared, could you start by telling us about the early days of the Menthol plant at Bushy Park?
Jared Klein: Certainly. When the plant was constructed back in 1976, it was designed with a certain capacity that remained largely unchanged for about two decades. During that time, we focused on small-scale projects to debottleneck and optimize existing processes without altering the core of the plant significantly.
What were some of the major changes that occurred after those initial two decades?
JK: In the late 90s and early 2000s, we began to see a need for expansion due to increasing demand. The first major upgrade was enhancing our D/L Menthol capacity. This involved installing new distillation systems and crystallizers, which significantly increased our L-menthol output as well.
Dr Peter Esser: Adding to that, we also revamped our isomerization and racemization processes. These areas were always part of the plant, but over the last twenty years, we've significantly increased their capacity and efficiency through technological upgrades and new installations.
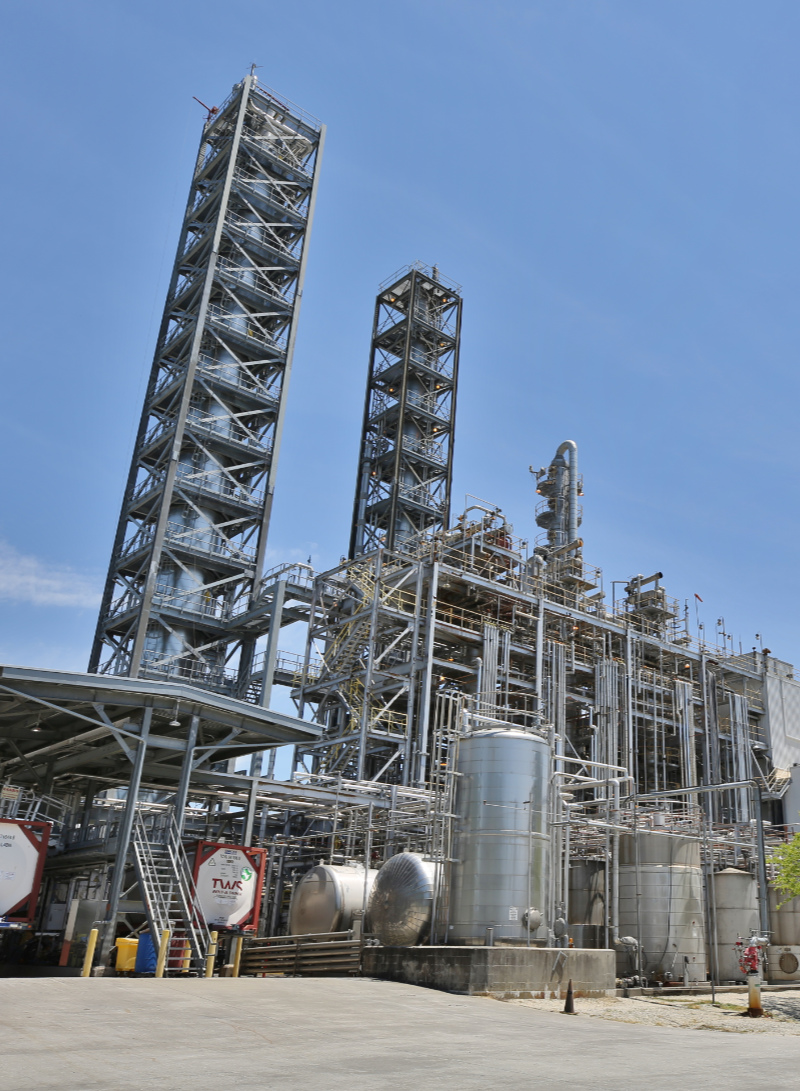
How does the Bushy Park facility compare with the one in Holzminden?
JK: One unique aspect of Bushy Park is its ability to complete the Menthol cycle. We can take D-menthol, sourced from Holzminden and/or Crude/Isomers from our business partner and convert it back into usable D/L or L-menthol. This capability allows us to be highly efficient and sustainable, recycling and reusing Menthol isomers within our own processes.
Could you elaborate on the technological advancements and innovations that have been integrated into the plant?
JK: Over the years, we've transitioned from batch operations to more continuous processes. This change has not only saved energy but also improved the consistency of our product. We've also implemented state-of-the-art control systems that allow for more precise operations, essential in continuous processing.
The market for Menthol has evolved as well. How has Bushy Park adapted to these changes?
JK: The Menthol market has indeed shifted significantly. Initially, we were primarily competing with natural Menthol sources, which are subject to variability due to agricultural conditions. However, as synthetic menthol production has increased globally, we've seen a shift. The competitive dynamics have indeed transformed significantly. Initially, our main competitors operated at a lower volume and used more costly processes. However, in the last 15 to 20 years, major players have entered the market, ramping up their production capacities to levels comparable to ours. This shift has spurred us to not only focus on increasing our production efficiency but also on enhancing the purity and consistency of our product. By leveraging advanced technologies and optimizing our processes, we've maintained a competitive edge, ensuring that we continue to meet the evolving demands of our customers and stay ahead in the market.
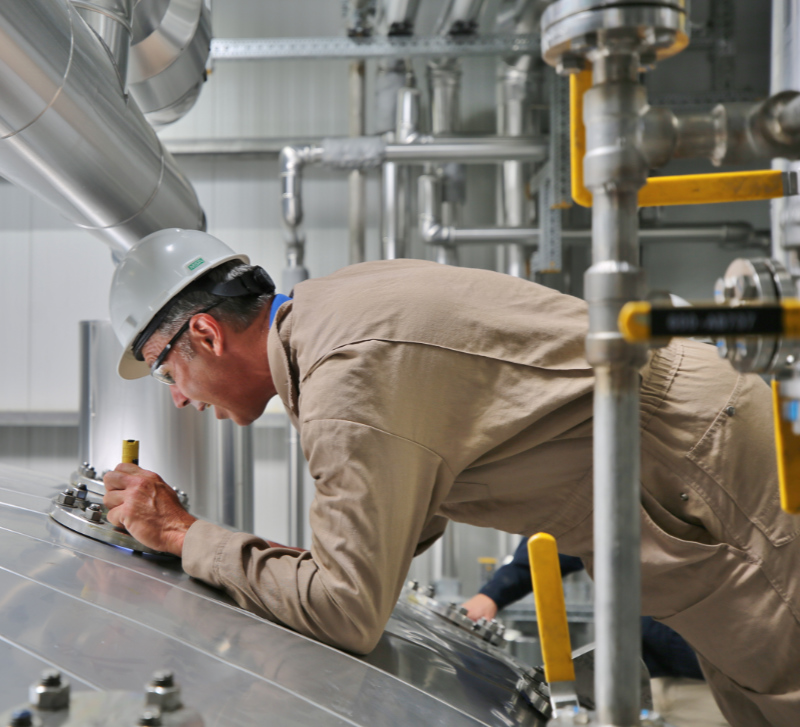
What about sustainability? How has Bushy Park addressed this critical issue?
PE: Sustainability is at the core of our operations. One of our major projects was to install an absorption chiller system that utilizes waste heat from distillation to generate refrigeration for the Menthol process. This improves our energy efficiency and actively reduces our carbon footprint for a more sustainable future
JK: And in terms of production, we've developed a solvent-free system for creating Menthol pellets, which significantly reduces our environmental impact compared to traditional methods.
PE: Over the years, we've also made significant strides in reducing our freshwater consumption. The transition to using vacuum technologies in our new equipment has been pivotal. These technologies allow us to operate without the need for large volumes of freshwater, which traditionally was necessary for cooling and other processes. This not only conserves water but also minimizes our wastewater production, aligning with our goals for environmental sustainability.
What are the next steps for Bushy Park or Symrise’s L-Menthol production in general?
PE: We are continuously exploring ways to enhance our efficiency and sustainability. This includes potentially adopting the Bushy Park processes at our Holzminden plant to unify our production capabilities and further reduce energy consumption. By streamlining our operations, we aim to minimize our environmental impact and contribute to a more sustainable future for the industry.
JK: Additionally, we are actively researching and developing methods to enhance our separation techniques with the goal to minimize the amount of material we need to purge from our system while still producing the highest quality product.