Frank Dannenberg and Burghard Rabe (right) have, in cooperation with their employees, taken many small steps that have led to great innovations.
“Never change a running system.” That could be the campaign slogan of Burghard Rabe, who oversees the spray-drying systems in the Symrise plants in Holzminden. Sensitive liquid flavor solutions, suspensions and pastes have been successfully turned into powders here for decades using high pressure and heat. But that isn’t enough for Rabe. “We want to keep improving, and that also means completely rethinking some steps in the process.”
The General Manager and a team of ten that includes technicians, spray-drying specialists and shift leaders get together in 2010 to prepare for taking a quantum leap forward. The objective at the time was the same across the company: become more efficient. The Flavors division introduced TPM as one way to achieve this. According to this method, small groups in individual departments take on the goal of uncovering potential at their workspace and, if it is deemed good, transfer this to the entire company.
Burghard Rabe and his team called one of their projects “Evoclean.” As the name suggests, this project is focused on the time it takes to clean the system. “We have to clean the system thoroughly for each of the roughly 1,300 products that we process,” the experienced employee explains. “That’s far from trivial. After all, we use flavors such as vanilla, garlic, raspberry and meat after each other – and having these tastes or scents transfer to the next product is definitely not something we want.” On top of that are the tight regulations for food products that call for absolute cleanliness.
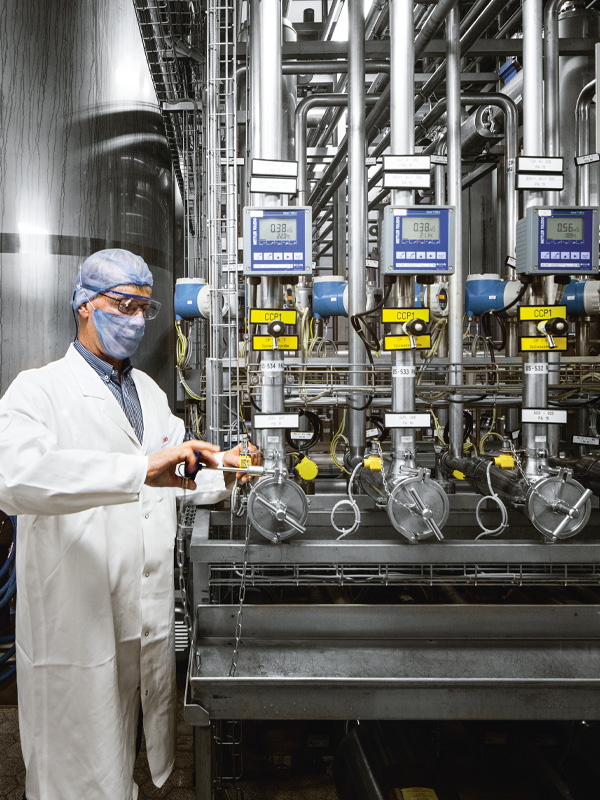
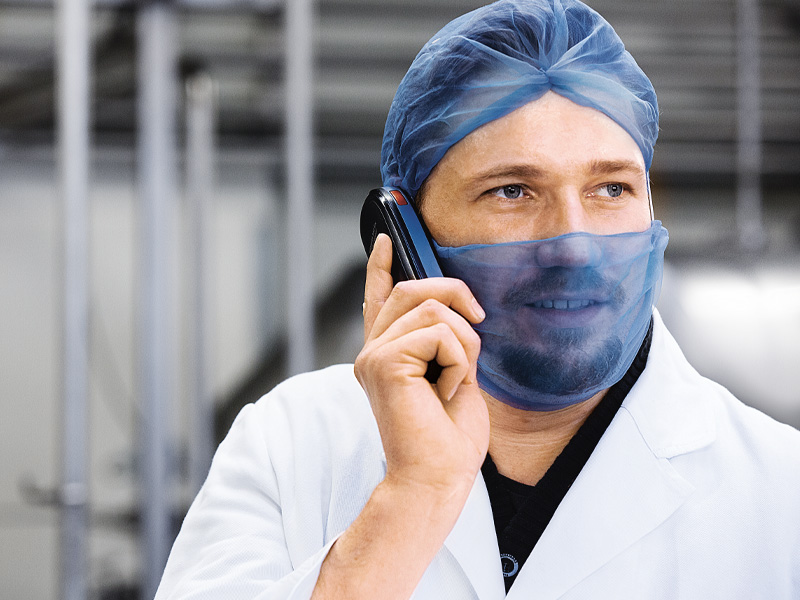
Moritz Welz, Production Foreman for Drying at the Solling plant, spends a lot of time with the systems – that provides him and his colleagues with the overview they need in order to push innovations.
Production comes to a halt during cleaning
The team, who knows the system down to the tiniest detail, went about this in small steps. “We took a close look at our ‘cleaning in place’ process. During this, cleaning is completely automated in the closed system,” Frank Dannenberg adds. Production Foreman for Drying at the Weser plant points to a valve node, the pipe lines and the shining silver spray chambers – systems that seem completely foreign to a layperson. “The cleaning solution has to run through all of those and then be washed out with water. One round takes up to six hours, during which no other products can be processed.” This means that roughly 20 to 30 % of the possible cycle of the eight spray-drying systems in both plants is lost for production. The experts gathered information at fairs, from customers and suppliers as well as online and came up with a number of approaches that they tested over time. The results are impressive. “We were able to reduce the cleaning time significantly,” says Frank Dannenberg.
The positive effects have an impact on sales as well as on cost and consumption – and thus also on the environment. “Each year, we are saving roughly 22,000 cubic meters of water (that means a reduction of 6.1 % per kg of product). We also now need about 1,500 tons less process steam, which corresponds to savings of about € 70,000. At the same time, weʼre reducing the CO2 output by about 300 tons, which equals 8.1 % less output per kg of product,” Moritz Welz, Production Foreman for Drying at the Solling plant, details. The costs for cleaning supplies could additionally be reduced by about € 100,000.
How that works specifically? By developing the technology further, for example. “After a lot of testing, we were able to replace the standard cleaning nozzles that had a diameter of about ten centimeters with nozzles that were a third that size. That reduces the amount of water that flows through and therefore the consumption with the same effect,” Welz explains. Symrise also took up negotiations with the producers of the cleaning supplies. The companies reviewed the processes together with the experts from Holzminden, tried out different products and concentrations of active ingredients. “By doing so, we were able to find the best solutions together – solutions that clean just as well but use fewer resources,” says Burghard Rabe. At the same time, the waste water load with phosphates, which were used in the old cleaning products, was reduced significantly.
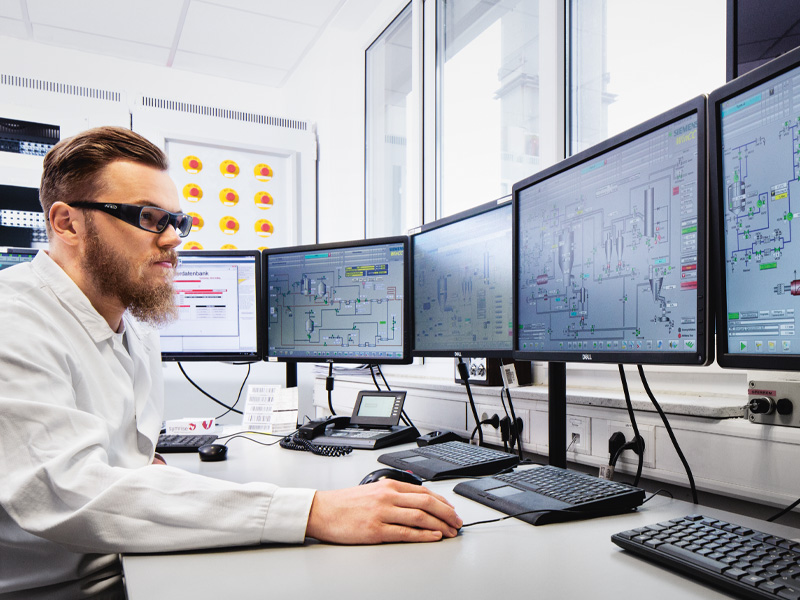
The employees in the control room manage the complex spray-drying systems and also check how the cleaning processes are going.
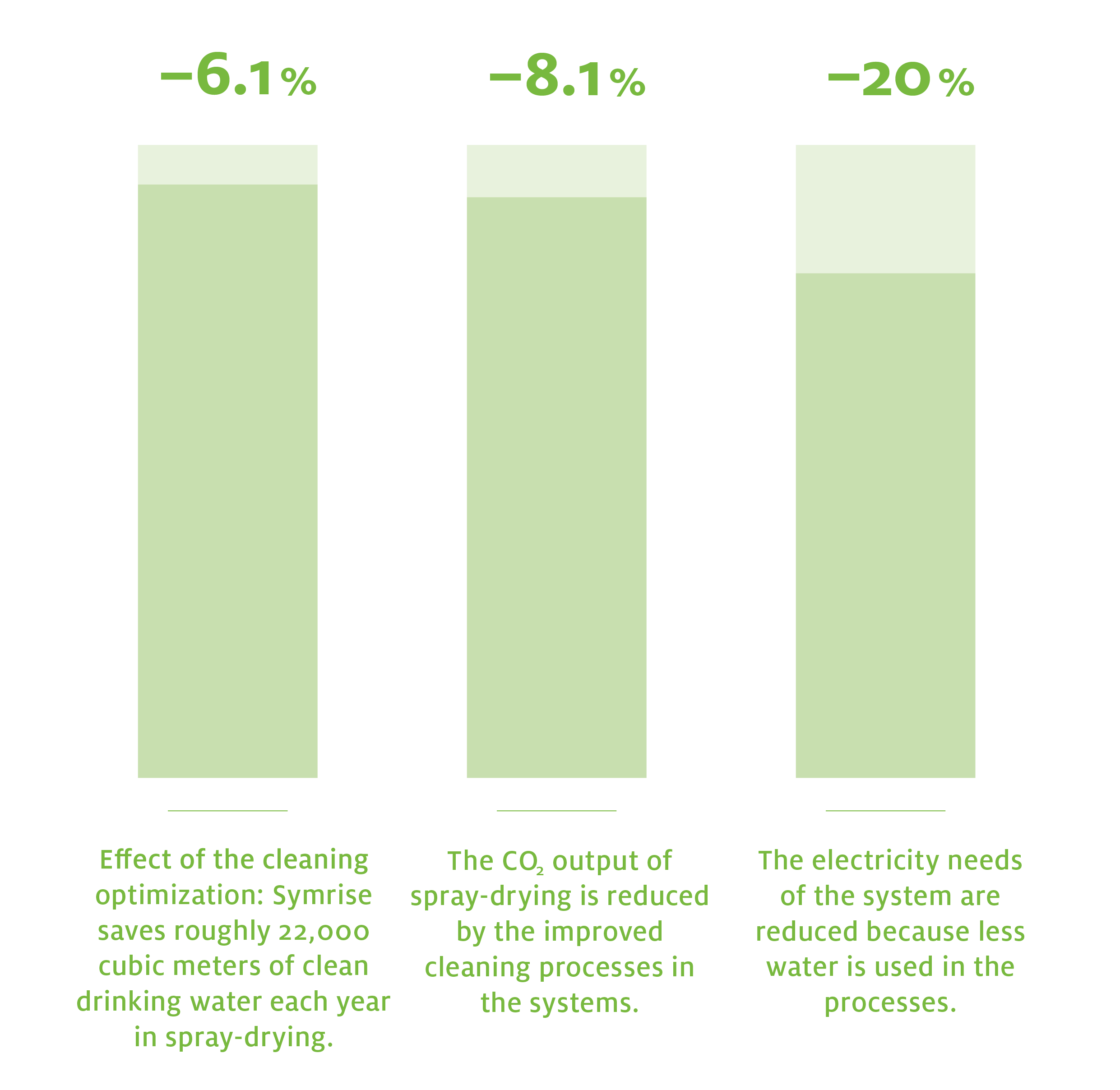
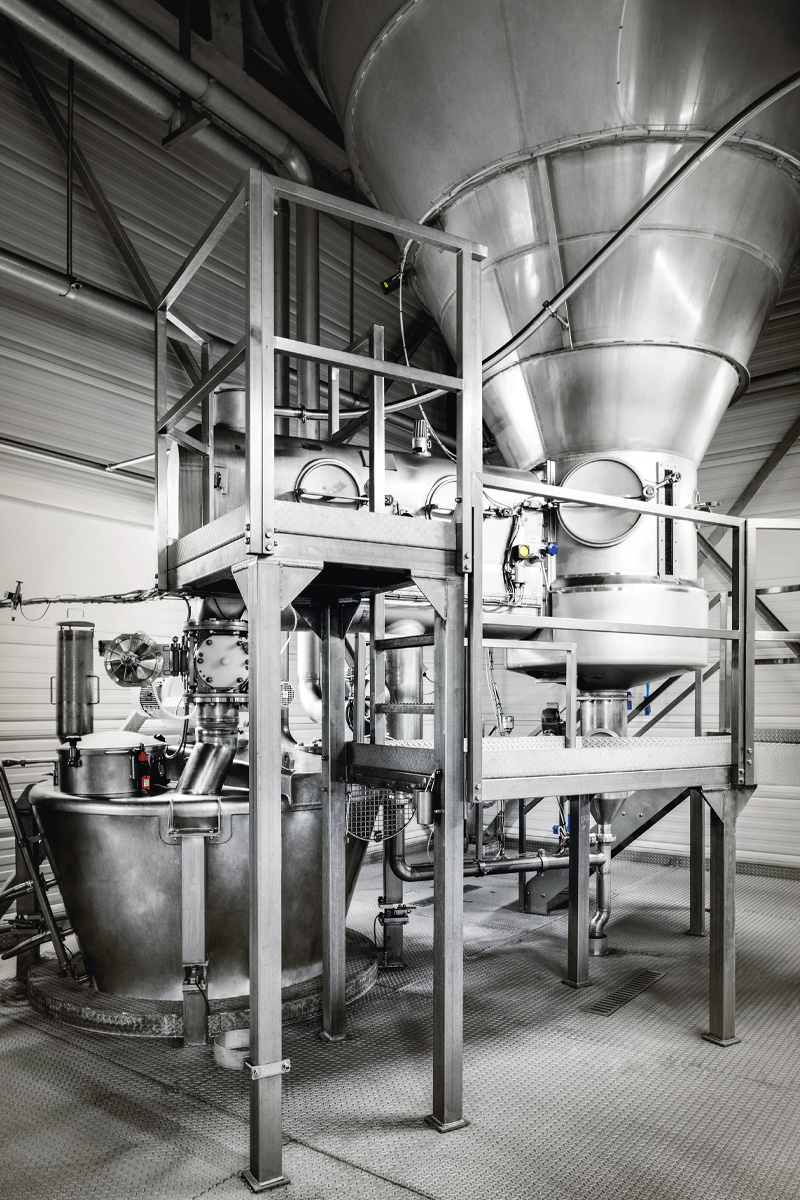
In the spraying tower, the flavor compositions with various carriers are fed into an airstream heated to 190 degrees Celsius. There they dry to tiny particles within seconds. The flavors are encapsulated that way, can be dissolved easily in the finished products and have an extremely long shelf life.
Improvements in production
A lot of know-how also went into the processes at the production level. In the vacuum dryer, the cooling water was reduced by more than 70 %, which equals 160,000 cubic meters. That’s enough water for more than one million baths. Water is also the key to optimizing the liquid preliminary stages for spray-drying. The less water there is in them, the less energy is needed to dry them. After a lot of experimenting, the water percentage could be reduced by up to 10 %. “In around 1,300 products, we were able to optimize the need for steam, electricity and compressed air and to reduce the need for energy by an average of 20 % in this way,” Rabe says, naming an additional impressive figure. The previous success helps Symrise in all the spray-drying processes in Holzminden; they will also be implemented at all the plants around the world in the future. And Burghard Rabe and his team have already turned their attention to other topics. In a pilot project, the employees are testing a new technology with which the energy for cleaning is no longer produced only by steam. Instead, it uses the condensation from spray-drying processes in a type of circuit system, Rabe explains. “Once the system is used in actual operations, we will save about 270 tons of CO2 each year.”
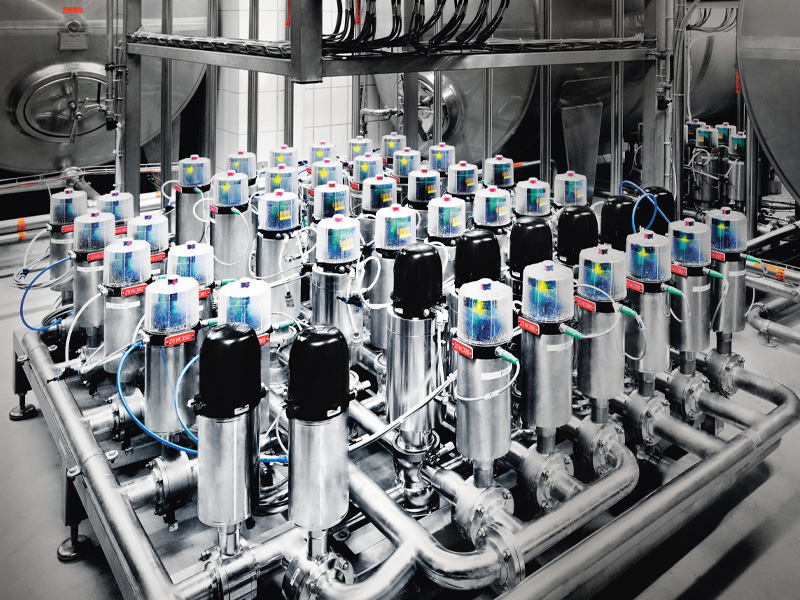
Transparency makes us strong
Mr. Körtner, you are closely linked with suppliers and customers through “Symchronize™”. Why have you taken this step?
We recognized about ten years ago that we weren’t efficient enough in our value chain. Companies usually take a look at their own processes when this happens. We did that, but it wasn’t enough. That’s why we brought key suppliers and customers on board for discussions. Since then, we’ve been synchronizing our shared supply chain more closely. We call these end-to-end supply chain solutions, which improve our supply chains sustainably.
How did you present this to the customers?
By showing them the benefits. We use “Symchronize™” in three clearly defined and transparent steps wherever we see high potential. That only works if everyone is open and willing to change something together. In the first step, which we call “Simplify,” we take a look at where we can change shared steps in the process that don’t create value. By analyzing need planning, inventory holdings and the ordering activity, for example, we are able to reduce our complexity in material supplies together. That alone saves us all about 20 %.
What happens next?
In the second step, called “Integrate,” we take a close look at the supply chain to the customer. Here we can achieve savings of between € 50,000 and € 2 million. We see, for example, how our customer processes our products and can use our expertise to optimize their processes. At the same time we avoid double work, for example in quality control. If we agree to shared inspection plans and methods, then the customer can save part of their comprehensive controls upon receipt of the goods, since we complete these checks anyway before shipping the goods out. We can also combine transportation to the customer, which reduces costs. The third step, “Collaborate,” involves a close look at the customer’s product development. If we know that the customer will be requiring a specific new product from us in the near future that contains a rare raw material, then we can order that material ahead of time. A lot of small measures add up to cost savings for the customer of up to 30 %.
Does Symrise also profit from this?
If a customer places their orders in an optimized way, then our process becomes streamlined and therefore also more cost efficient. It additionally allows us to manage our production better once we have exact target figures. We also have advantages because our own suppliers understand our expectations better and can help to improve our products. That has proved to be the case each time in the 50 comprehensive projects we have already completed.
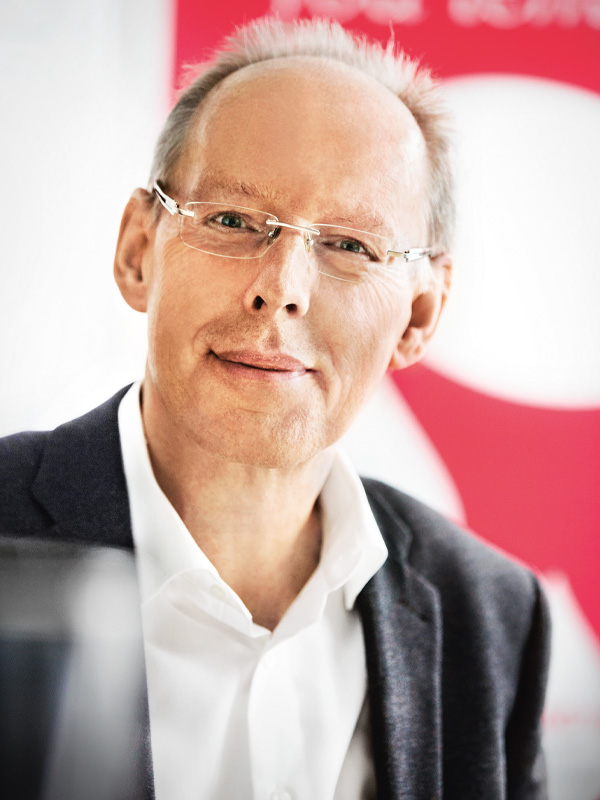
Bernd Körtner manages programs to increase efficiency in the Operations Flavors department at Symrise. One of these is Symchronize™ which is based on a close linking of the cross-company supply chain.
-3 to -7%
The process costs could sink between € 50,000 and € 2 million per customer.