Greg Clements reaches for one of the light-green pine branches. He removes a needle from the two-year-old tree, which stands just as tall as him, and sniffs the fresh scent. Then Clements turns around. Perfectly arranged rows of small conifers growing in the sandy soil stretch as far as the eye can see. A hundred meters in the other direction lies another similarly arranged pine forest of trees planted over 20 years ago – these trees are now ready to be harvested. Here at the northern edge of Florida, the technical manager for strategic raw materials is looking at the origin of many Symrise products. These forests produce pinewood, which is rich in terpenes, an ingredient that is the initial building block for our aroma and fragrance materials. The trees will first be processed in a paper factory using the Kraft process. The Kraft pulping process produces a byproduct called crude sulfate turpentine (CST), which is the starting material for Symrise’s terpene-based fragrance and flavor ingredients. The technology for the fractionation of CST into alpha and beta pinene and the extraction of sulfur was developed by the US company Renessenz, which has a rich history of over 100 years of innovation and production. As part of Pinova Holdings, Renessenz was acquired by Symrise at the beginning of 2016. To get an overview of what we do, says Clements, it helps to start at the plantation. “It is important to us that we use a sustainable raw material to create equally sustainable products.” The foresting company that owns the plantation, for instance, produces the wood in a sustainable cycle, certified according to the standards of the Sustainable Forestry Initiative (SFI). Other suppliers use the seal of the Forest Stewardship Council (FSC).
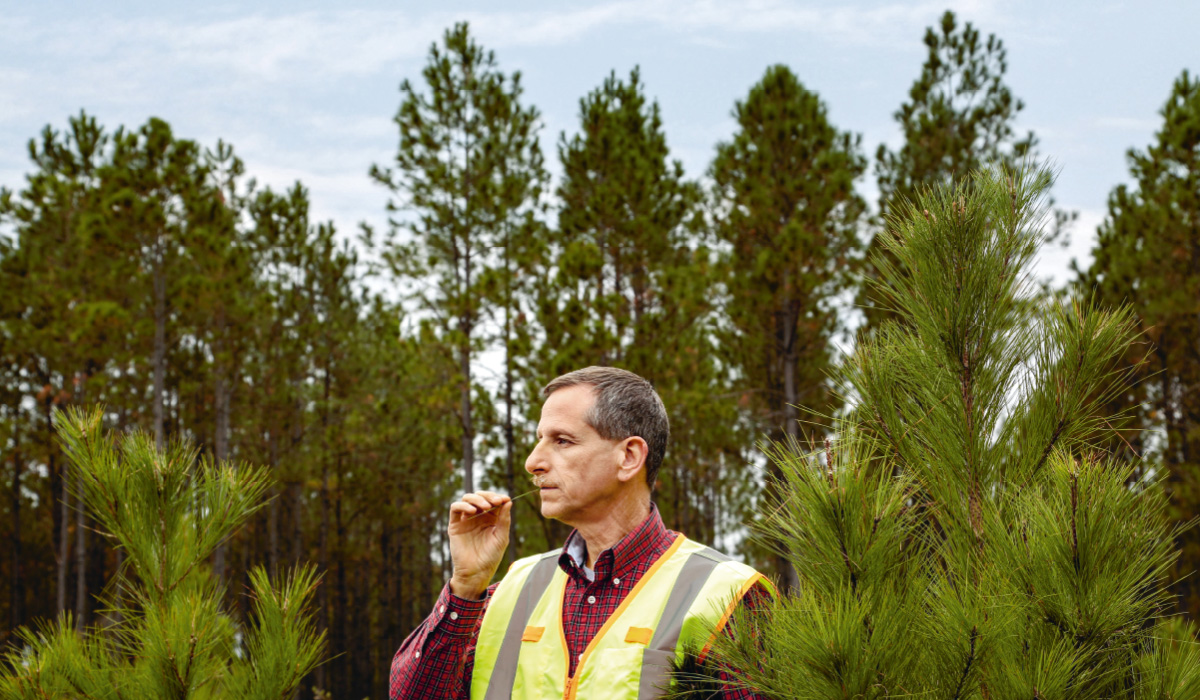
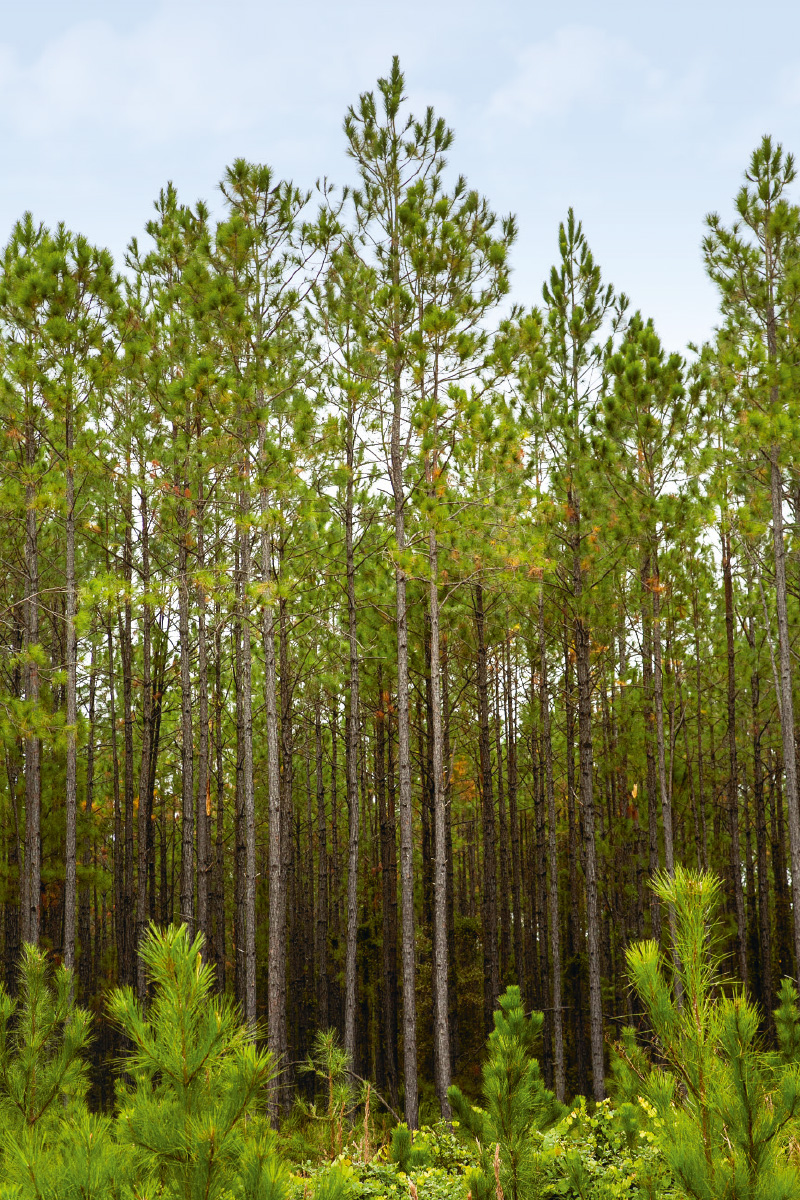
“It is important to us that we use a sustainable raw material to create equally sustainable products.”
Greg Clements
Engineer
A portion of the trees go to the pulp factory. Greg Clements works closely with around 40 of these factories. He worked in the industry for many years and knows all the processing steps. In his current position, he is mainly involved in optimizing the extraction of crude sulfate turpentine (CST). The viscid, flammable liquid, which has a sulfuric smell, used to be burned as a waste product. Today, Symrise is reusing it.
“The paper factories know their business very well,” says Clements. “Together, though, we can optimize processes to get the highest possible yield of CST.” At the end, the product is stored in tanks that Symrise transports back to its factory in Jacksonville using trucks and railroad cars. “Our logistics are an unbeatable advantage for the paper factories,” says Greg Clements. “The storage options for CST at the paper mills are very limited. We help the factories manage the supply chain of their byproducts reliably while simultaneously securing our raw materials basis.”
The expertise needed to find the best scent molecules
The multistep chemical process begins at the massive Symrise plant covering roughly 50 hectares. To start, the sulfur and other substances that can be used as fuels are removed from the CST via a strip distillation process, which the company developed. They provide about 50 % of the fuel that Symrise needs to generate steam. Richard Hastings manages the plant together with his team. The experienced Plant Manager has been working at the Jacksonville site for 37 years and knows the distillation and extraction systems like the back of his hand. He stands in front of a five-pillared reactor that runs around the clock. Gesturing energetically, he explains how the purified CST is separated in a continuous process into its main components – the terpenes alpha-pinene and beta-pinene. With further processing methods like hydrogenation or pyrolysis, Symrise primarily uses the higher volume alpha-pinene to create fragrant molecules such as dihydromyrcenol, linalool (Symrise is the only manufacturer that produces this from renewable sources), citronellol or geraniol.
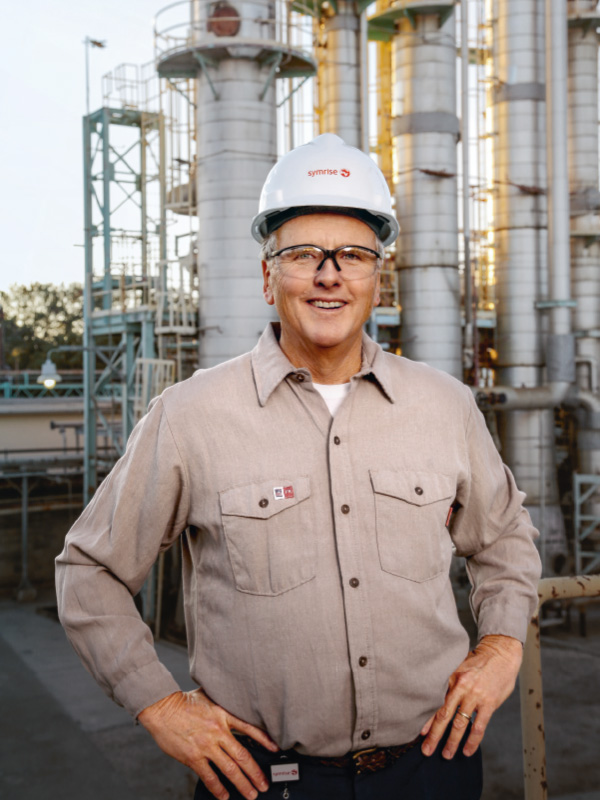
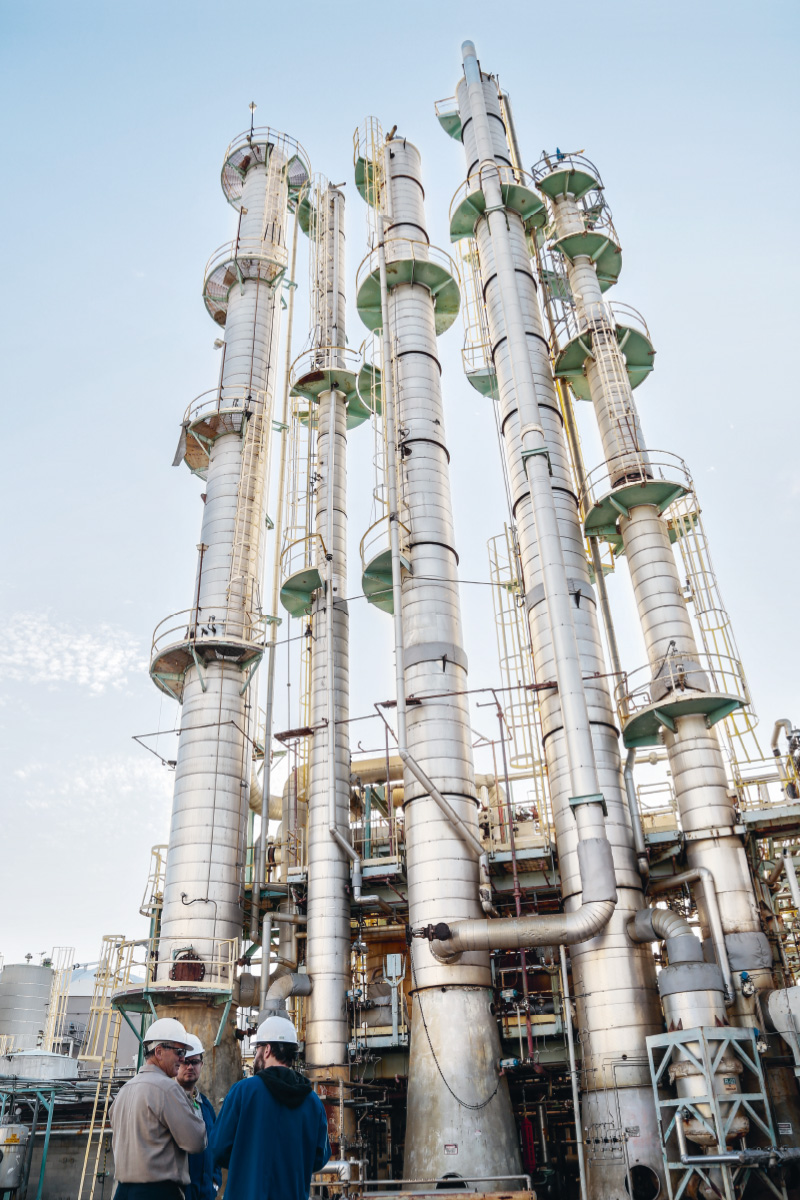
Process expertise
Richard Hastings has the chemical processes well in hand at the Symrise factory in Jacksonville, which covers approximately 50 hectares. The Plant Manager ensures continuous operation day and night of the distillation and extraction systems, one of which separates purified crude sulfate turpentine into its main components alpha-pinene and beta-pinene.
It is truly remarkable to see the processes that have developed here over the years.Peter Esser, Vice President of Global Chemical Production
Generating fragrant substances from the byproducts of paper production sounds like a small miracle. For Gene Kolomeyer, Head of Research and Development in Jacksonville, it is a simple process technology. The experienced chemist, who has been working at Symrise for 20 years, says this with a broad smile. He knows that it took decades for his predecessor and him to refine the processes to this point. He explains, “The basic material remains the same, with its ten carbon atoms. We just modify it and recompose it. That isn’t magic – it just takes very detailed expertise regarding the various temperatures, pressures, volumes, process speeds and durations to produce the best results.”
More efficiency, more sustainability
Peter Esser, who relocated to Jacksonville with the acquisition in early 2016, is focusing on process optimization. When he first came to visit the production site in sunny Florida, the Vice President of Global Chemical Production for Symrise plants in the USA, Mexico and Holzminden encountered
a great deal of know-how and process-development experience here. “It is truly remarkable to see the processes that have developed here over the years. We are now putting our heads together to make production even more sustainable and efficient,” Esser says.
For example, Symrise is investing in equipment automation. “By doing this we can check all the parameters in the process every few seconds and make immediate adjustments if necessary,” Esser explains. Processes are being reviewed systematically and analytically. “We review catalysts, processing steps as well as process technologies so we can create our products in a more efficient and sustainable way. This starts with the fractionation of CST and is followed by the optimization of processes for individual products.” Initial results of this systematic approach can already been seen, while other process optimization measures are part of the longer-term strategy.
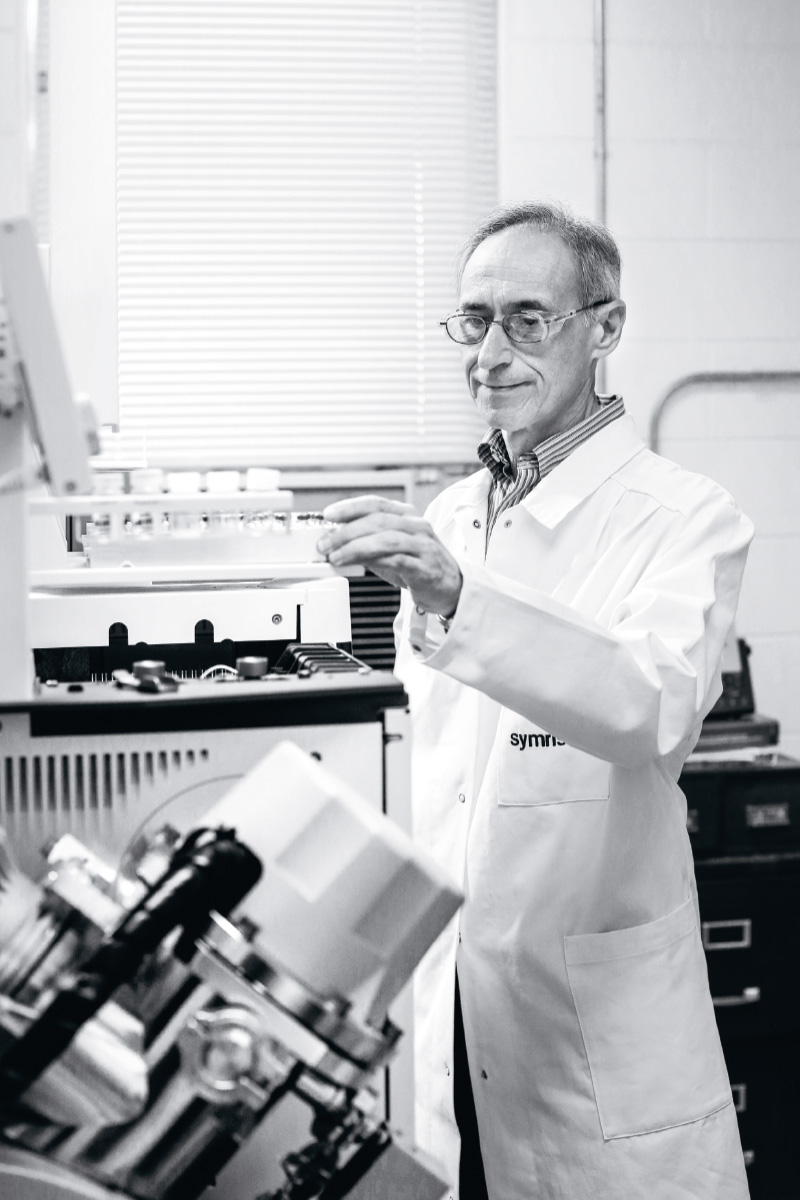
Know-how in research
Gene Kolomeyer and his team are always working on new products and processes in the Symrise laboratories. The Head of Research and Development can draw on the company’s extensive know-how.
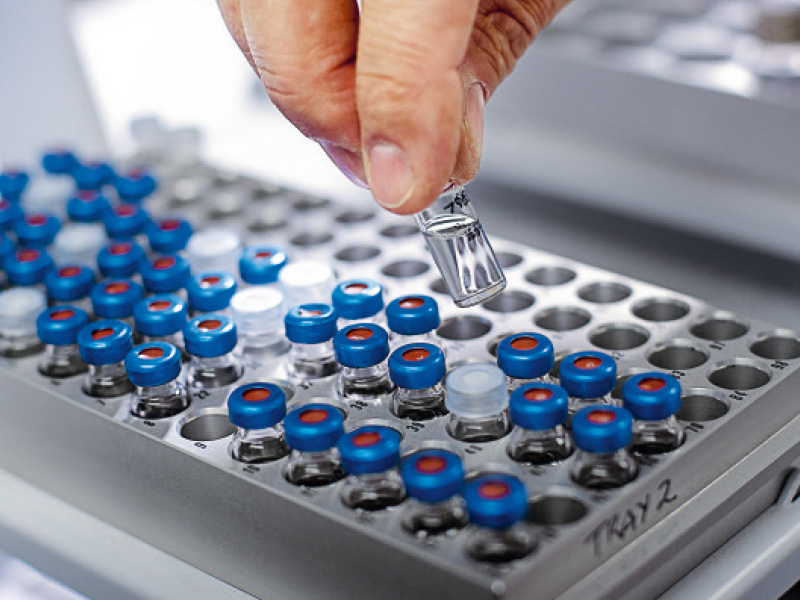
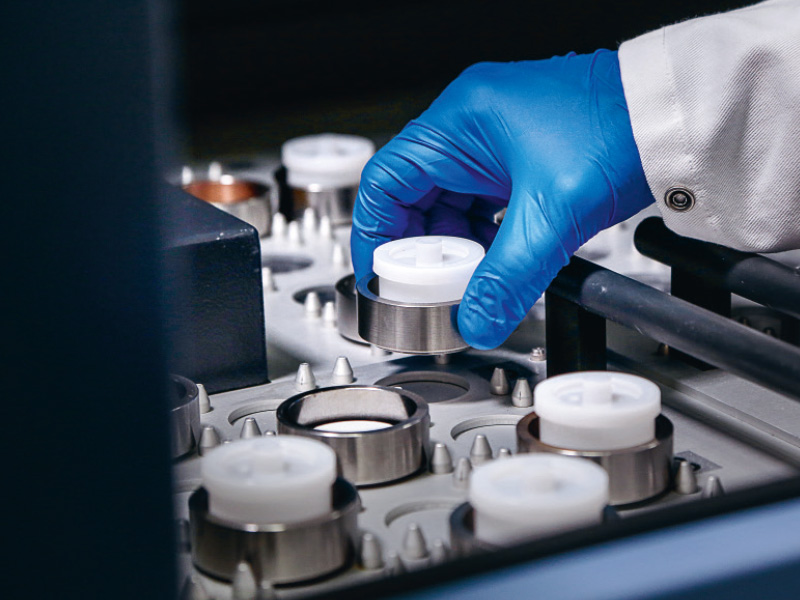
As well as using CST as a raw material, the team is also working on similar processes for other raw materials. Symrise uses the naturally occurring substance D-limonene, which comes from the oil extracted from orange peel in orange juice production, for example. “Again, in this case we use a substance that occurs as byproduct and was previously discarded as waste,” Peter Esser explains. Symrise produces L-carvone from limonene using a patented green technology that is significantly environmentally friendlier than the traditional process for producing L-carvone. L-carvone is used in oral care applications together with anethole, sensory coolants that are also made by the company in Jacksonville.
Symrise products found around the world
“These products perfectly complement Symrise menthol derivatives made in Bushy Park, South Carolina, and Holzminden, Germany, and make Symrise the number one industry supplier of oral care ingredients,” Michael Klamm says, describing the importance of the portfolio. “We’re also one of the biggest players in the industry when it comes to the production of scent molecules from CST.” Klamm is in charge of global business support for the Aroma Molecules division and heads up the plants in Jacksonville and Colonels Island. He knows all the ins-and-outs of the market. “We supply all the large scent and flavor manufacturers as well as consumer packaged goods manufacturers. Our ingredients are often some of the most pronounced elements in our customer’s scent and flavor compositions,” Klamm says. He doesn’t know exactly how many households our molecules provide with pleasant fragrances. “You can find our ingredients in many perfumes, home and laundry care, cosmetics as well as oral care applications. Our products are integral ingredients in well-known brands that play a big role in consumers’ lives.” A considerable portion of the products goes to other Symrise plants, where the molecules are used in fragrance and flavor compounds. “The purchase of Renessenz suits Symrise’s portfolio perfectly,” Klamm says. “Our product portfolio covers a wide variety of ingredients used by Symrise perfumers and flavorists.” The production’s sustainability also plays an important role for customers. “Products made from natural renewable feedstock, which are byproducts of other industries, have been the starting point of our production for over 100 years. We use natural resources and green chemistry,” says Michael Klamm, “which is becoming more and more important to our customers, who are increasingly demanding sustainable products.”
“We use natural resources and green chemistry.”
Michael Klamm Senior Vice President and General Manager
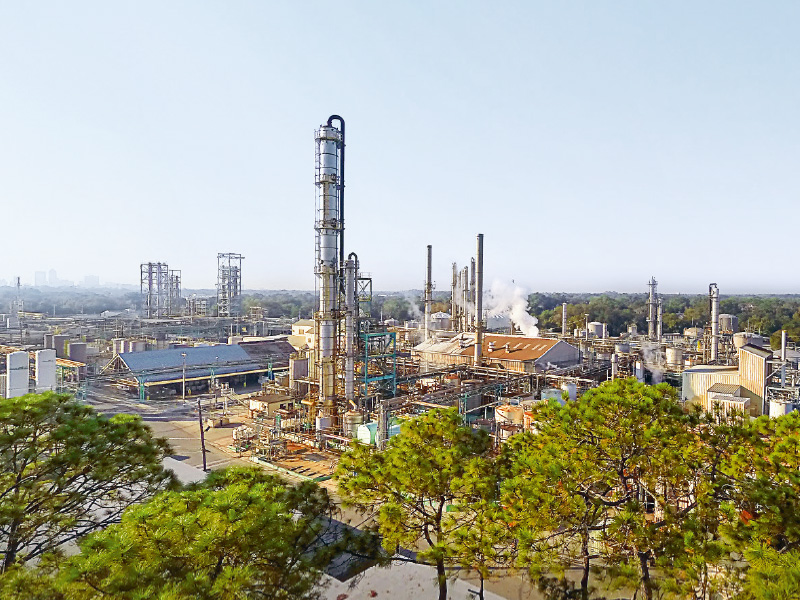
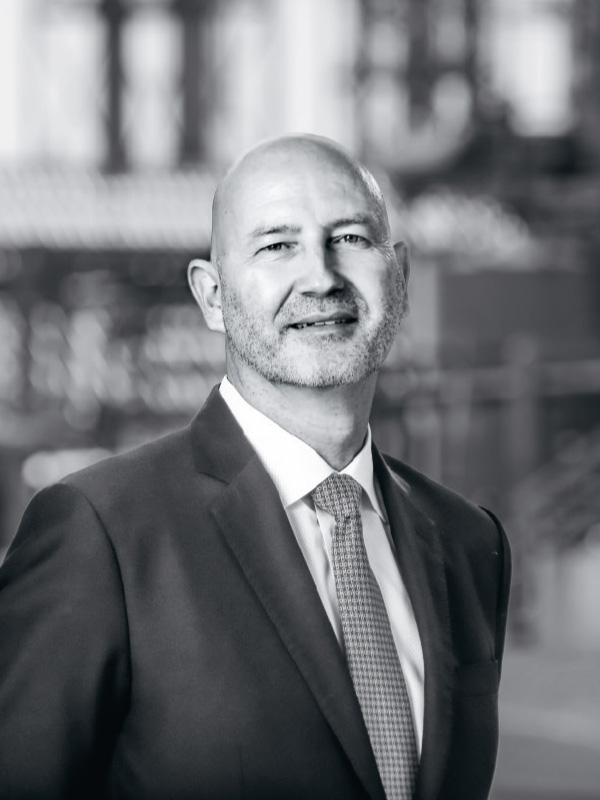
Product diversity
The Symrise factory in Jacksonville also uses other raw materials in addition to crude sulfate turpentine, a byproduct from the paper industry. For instance, L-carvone is produced from the natural substance D-limonene, which comes from the oil in orange peels. This product is used in oral care applications.
For the environment. For safety.
The predecessor company to Renessenz and Symrise was established in Jacksonville in 1910. It manufactured resin originally used in the naval industry for sealing wooden boat hulls. This led to more products being developed, and in the 1950s and 1960s the first substances for the fragrances and flavors industry came about. Using the raw material CST from the paper industry has been a challenge because even the slightest traces of the unpleasant sulfurous odor, which it emitted, can impact the environment and the neighborhood.
“Self-responsibility is part of our work culture and is vastly important in achieving our goals.”
Brian Zielinski
Environmental Manager
“Constant process and handling improvements are necessary to eliminate emissions and ultimately the effect on the environment and neighbors,” says Corporate Compliance Director Brenda Murray. “Over the years we have installed sophisticated filters and tanks, optimized internal transport routes and identified potential leaks to prevent odor from escaping.” A whole range of certificates prove its efficacy – and above all, the employees are cued to watch out for any irregularities that could occur in production. “This self-responsibility is part of our work culture and is vastly important in achieving our goals,” adds her colleague Brian Zielinski, who works as an Environmental Manager at the Jacksonville site.
Preventing accidents in the workplace is just as important. According to health and safety manager, Bert Long, a broadly implemented program has increased awareness of this topic. “We record even minor unsafe situations and potential dangers.” This has led to a safety culture where everyone looks out for each other. Brian Zielinski demonstrates how environmental awareness and business success go hand in hand. Since 2015, Symrise has cut the wastewater produced at the Jacksonville plant on a daily basis by more than half – that’s around one million liters. This is the result of a sustainability project that took the entire system back to the drawing board. “We switched off a large number of pumps that were not needed for every task. They had previously run continuously and used water that we are now saving.”
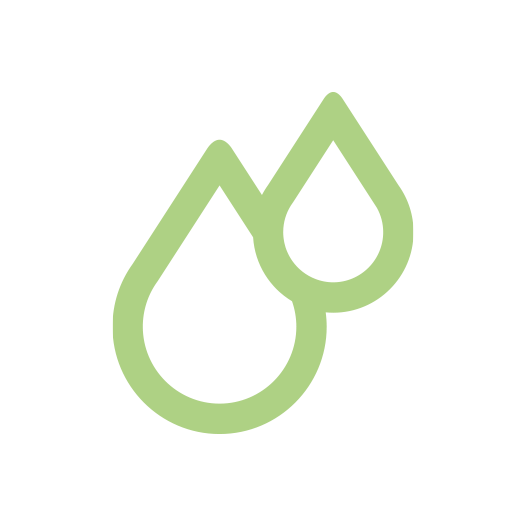
1 million liters
the amount of wastewater avoided at the Jacksonville factory every day