Frank Dannenberg und Burghard Rabe (re.) haben gemeinsam mit ihren Mitarbeitern in vielen kleinen Schritten für große Innovationen gesorgt.
„Niemals ein laufendes System verändern“, könnte der Wahlspruch von Burghard Rabe lauten. Der 61-Jährige leitet die Sprühtrocknungsanlagen in den Symrise Werken in Holzminden. Mit hohem Druck und Hitze werden hier seit Jahrzehnten erfolgreich empfindliche flüssige Aromenlösungen, Suspensionen oder Pasten in Pulverform gebracht. Doch das ist Rabe nicht genug: „Wir wollen uns stetig verbessern, und das heißt auch, manche Prozessschritte ganz anders zu denken.“
Zu einem Quantensprung haben der Betriebsleiter und ein zehnköpfiges Team aus Technikern, Sprühtrocknungsmeistern und Schichtleitern im Jahr 2010 angesetzt. Die Vorgabe damals hieß wie überall im Unternehmen: effizienter werden. Als einen Weg dahin hat der Geschäftsbereich Flavors TPM eingeführt. Kleine Gruppen in einzelnen Abteilungen sollten an ihrem Arbeitsplatz Potenziale entdecken und, wenn sie für gut befunden wurden, auf den gesamten Konzern übertragen.
Burghard Rabe & Co. nannten eines ihrer Projekte „Evoclean“, das sich, wie es der Name schon andeutet, mit den Reinigungszeiten der Anlage beschäftigt. „Für jedes unserer rund 1.300 Produkte, das wir verarbeiten, müssen wir das System gründlich säubern“, erzählt der erfahrene Mitarbeiter. „Das ist gar nicht so trivial: Immerhin nutzen wir Aromen wie Vanille, Knoblauch, Himbeere oder Fleisch nacheinander – und eine Übertragung der Geschmäcker oder Gerüche ist natürlich überhaupt nicht erwünscht.“ Hinzu kommen die enorm strengen Vorgaben für die Lebensmittelproduktion, nach denen absolute Sauberkeit gefordert ist.
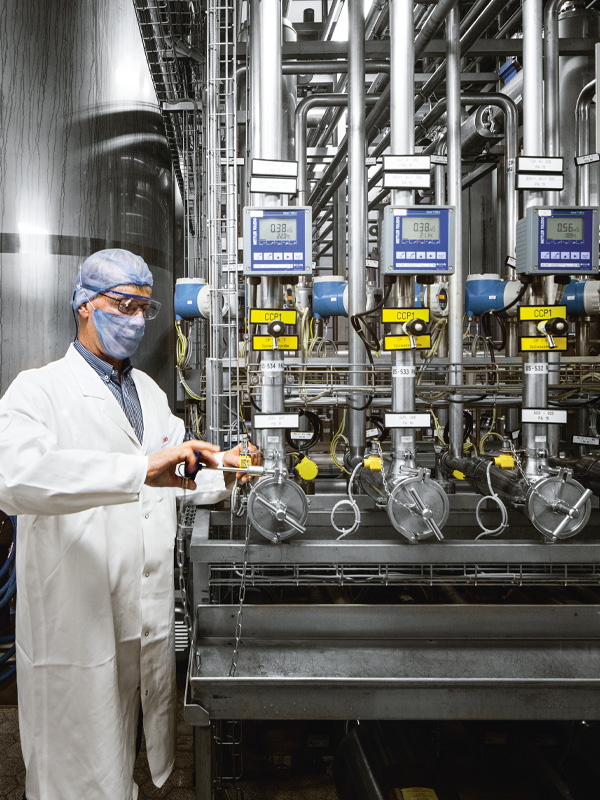
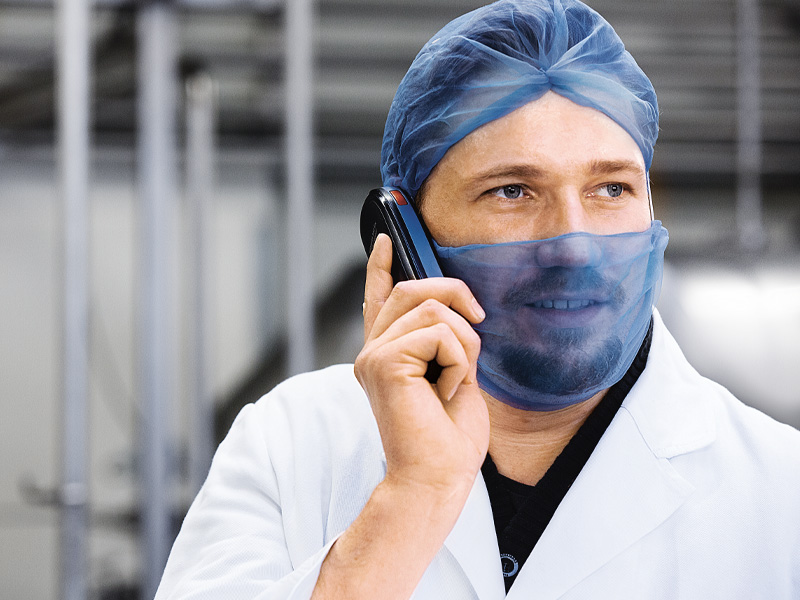
Moritz Welz, Produktionsmeister Trocknung des Werks Solling, verbringt viel Zeit in der Anlage – nur so erhalten er und seine Kollegen die nötigen Einblicke, um die Neuerungen voranzutreiben.
Produktion steht während der Reinigung still
Das Team, das die Anlage bis ins kleinste Detail kennt, ging in kleinen Schritten vor. „Wir haben uns unseren sogenannten ,Cleaning in Place’-Prozess genau angeschaut. Die Reinigung wird dabei in der geschlossenen Anlage vollautomatisch vorgenommen“, ergänzt Frank Dannenberg. Der Produktionsmeister Trocknung des Werks Weser zeigt auf einen für den Laien unübersichtlichen Ventilknoten, auf die Rohrbahnen und die silbern glänzenden Kessel. „Dort überall muss das Reinigungsmittel durch und mit Wasser nachgespült werden. Ein Durchgang dauerte bis zu sechs Stunden, in denen zwangsläufig kein anderes Produkt verarbeitet werden konnte.“ Rund 20 bis 30 % der möglichen Laufzeit der insgesamt acht Sprühtrocknungsanlagen in den beiden Werken fielen also für die Produktion aus. Die Experten informierten sich auf Messen, bei Kunden und Zulieferern oder auch im Internet, überlegten sich mehrere Ansätze, die sie im Laufe der Zeit testeten. Das Ergebnis ist beeindruckend. „Wir konnten die Reinigungszeit merklich reduzieren“, sagt Frank Dannenberg.
Die positiven Effekte wirken sich auf der Umsatz- sowie auch auf der Kosten- und Verbrauchsseite aus – und damit für die Umwelt. „Wir sparen pro Jahr rund 22.000 Kubikmeter Trinkwasser (das bedeutet eine Reduktion von 6,1 % pro kg Endprodukt). Außerdem benötigen wir ca. 1.500 Tonnen Prozessdampf weniger, das entspricht einer Einsparung von rund 70.000 €. Damit reduzieren wir gleichzeitig den CO2-Ausstoß um rund 300 Tonnen, das heißt 8,1 % geringerer Ausstoß pro kg Endprodukt“, beschreibt Moritz Welz, Produktionsmeister Trocknung des Werks Solling, die Fakten. Außerdem konnten die Reinigungsmittelkosten um rund 100.000 € verringert werden.
Wie das im Einzelnen funktioniert? Mit einer technischen Weiterentwicklung zum Beispiel. „Nach vielen Tests konnten wir die üblichen Reinigungsdüsen mit einem Durchmesser von rund zehn Zentimetern gegen ein Drittel kleinere Düsen austauschen. Das reduziert bei gleicher Wirkung den Wasserdurchfluss und damit auch den Verbrauch“, erzählt Welz. Ebenso trat Symrise in Verhandlungen mit den Reinigungsmittelherstellern. Die Firmen schauten sich gemeinsam mit den Experten aus Holzminden die Prozesse an, probierten verschiedene Produkte und Wirkstoffkonzentrationen aus. „Dadurch konnten wir gemeinsam optimale Lösungen finden, die ebenso sauber spülen, aber weniger Ressourcen verbrauchen“, sagt Burghard Rabe. Zugleich wurde dabei die Abwasserbelastung mit Phosphaten, die in den alten Reinigungsmitteln verwendet wurden, erheblich gesenkt.
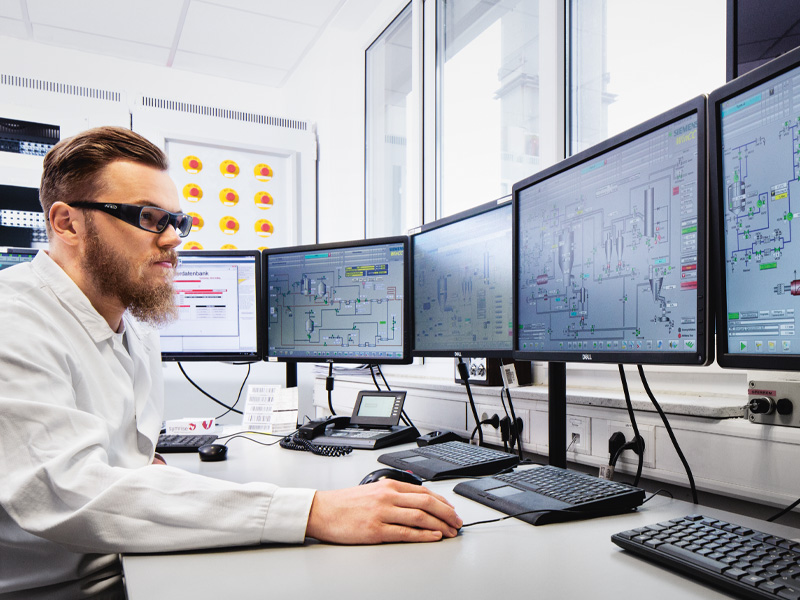
Die Mitarbeiter in der Leitwarte steuern die komplexen Sprühtrocknungsanlagen und überprüfen dabei auch, wie die Reinigungsprozesse ablaufen.
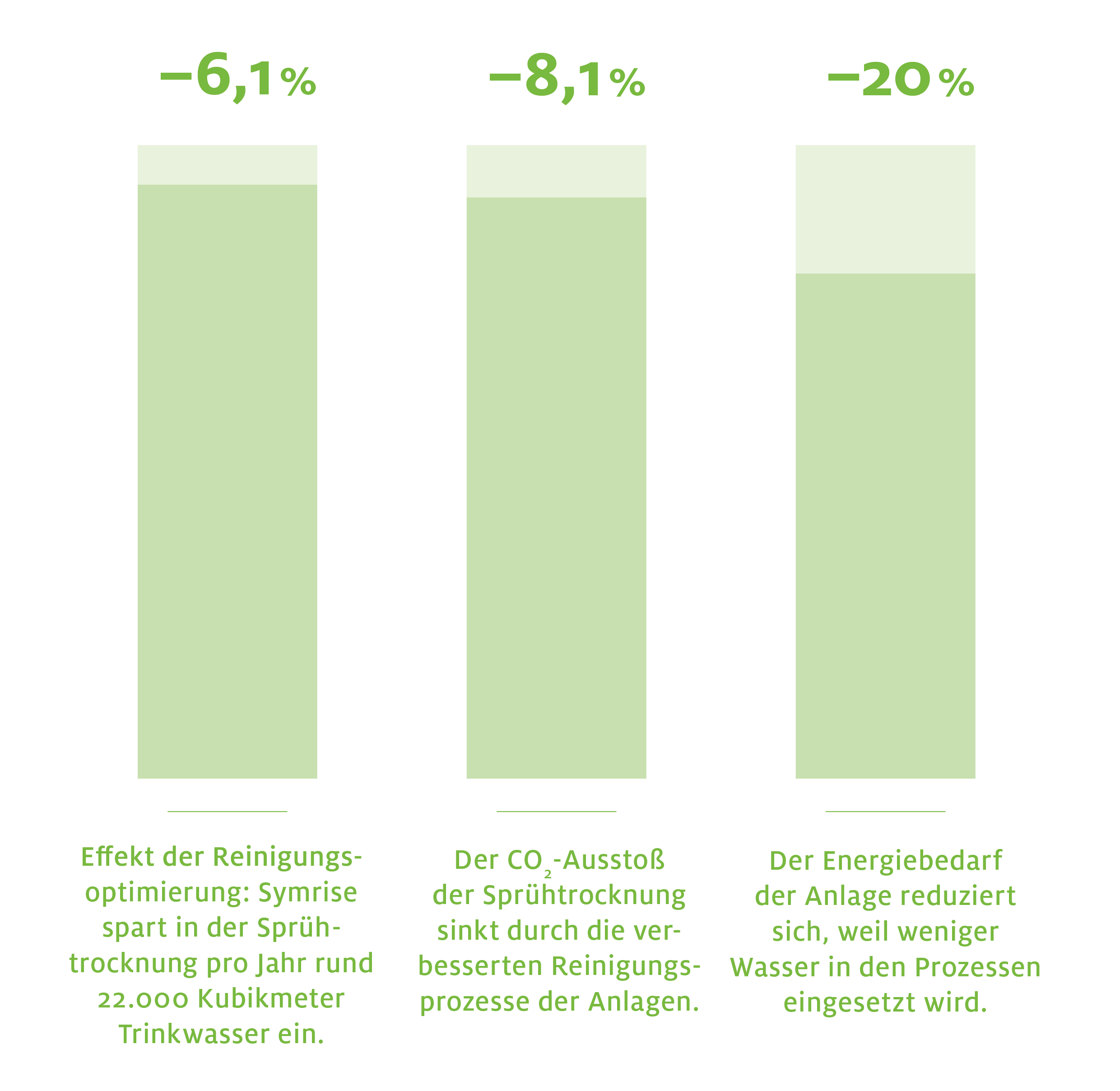
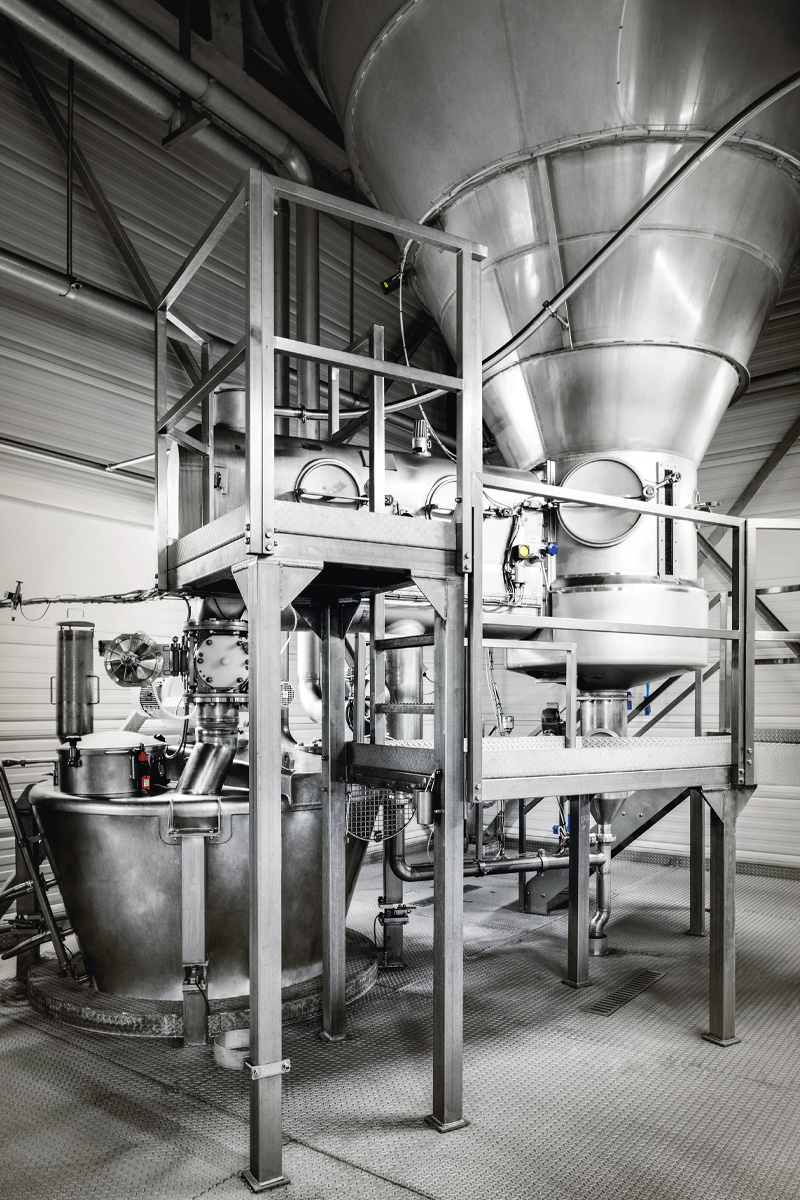
Im Sprühturm werden die Aromenkompositionen mit verschiedenen Trägerstoffen in einen 190 Grad Celsius heißen Luftstrom geleitet. Dort trocknen sie in Sekundenschnelle zu kleinen Partikeln. Die Aromen werden so eingekapselt, sind später in den Endprodukten leicht lösbar und extrem lange haltbar.
Verbesserungen in der Produktion
Auf der Produktionsebene floss ebenso großes Know-how in die Prozesse mit ein. Im Vakuumtrockner wurde das Kühlwasser um mehr als 70 % und damit um 160.000 Kubikmeter zurückgefahren – das reicht für mehr als eine Million Vollbäder. Um das Wasser geht es auch bei einer Optimierung der Flüssigvorstufen für die Sprühtrocknung. Je weniger Wasser in ihnen vorhanden ist, umso weniger Energie ist zwangsläufig nötig, um sie zu trocknen. Mit Hilfe vieler Experimente konnte der Wasseranteil um bis zu 10 % gesenkt werden. „Bei rund 1.300 Produkten haben wir so den Bedarf an Dampf, Strom und Druckluft optimiert und den Energiebedarf insgesamt um durchschnittlich 20 % reduziert“, nennt Rabe einen weiteren beachtlichen Wert. Die bisherigen Erfolge helfen Symrise in sämtlichen Sprühtrocknungsprozessen in Holzminden, die Übertragung auf die Werke in aller Welt steht an. Und Burghard Rabe und sein Team haben sich bereits neue Themen vorgenommen. In einem Pilotprojekt probieren die Mitarbeiter eine neue Technologie aus, mit der die Energie für die Reinigung nicht mehr nur per Dampf bereitgestellt wird. Sie nutzt stattdessen das Kondensat des Sprühtrocknungsprozesses in einer Art Kreislaufsystem, erklärt Rabe. „Wenn das System erst einmal im Echtbetrieb angewendet wird, können wir rund 270 Tonnen CO2 im Jahr einsparen.“
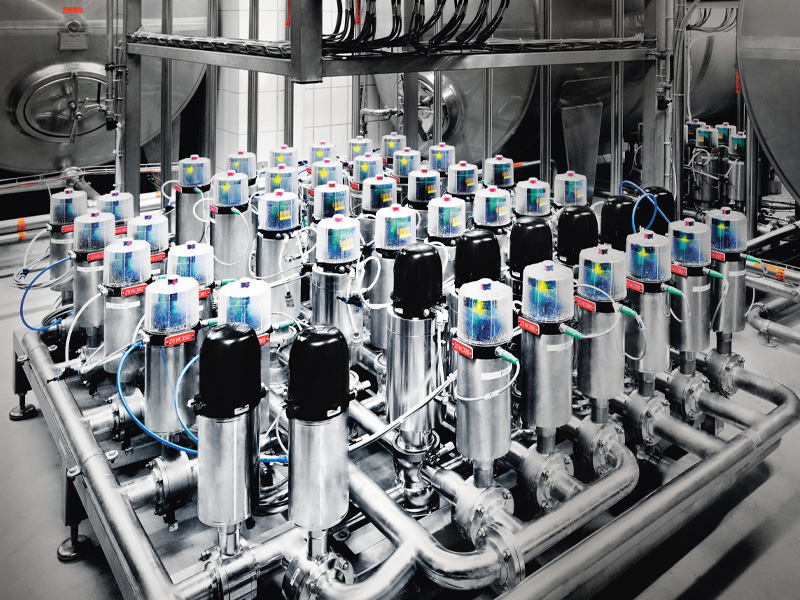
Transparenz macht stark
Herr Körtner, mit „Symchronize™“ vernetzen Sie sich sehr intensiv mit Zulieferern und Kunden. Warum sind Sie diesen Schritt gegangen?
Wir haben vor etwa zehn Jahren festgestellt, dass wir in unserer Wertschöpfungskette nicht effizient genug waren. Typischerweise schauen sich Unternehmen dann ihre eigenen Prozesse an. Das haben wir auch gemacht, es reichte aber nicht. Deswegen haben wir wichtige Zulieferer und Kunden mit ins Boot geholt. Seitdem synchronisieren wir die gemeinsame Supply Chain stärker. Wir sprechen hier von End-To-End Supply Chain Lösungen, durch die wir unsere Versorgungsketten nachhaltig verbessern.
Wie haben Sie das den Kunden vermittelt?
Indem wir ihnen die Vorteile gezeigt haben. „Symchronize™“ wenden wir in drei klar definierten und transparenten Schritten immer dort an, wo wir ein hohes Potenzial sehen. Das funktioniert nur, wenn sich alle Beteiligten öffnen und gemeinsam bereit sind, etwas zu verändern. Im ersten Schritt, den wir „Simplify“ nennen, schauen wir darauf, wo wir gemeinsam Prozessschritte verändern können, die nicht wertschaffend sind. Wir können durch die Analyse etwa von Bedarfsplanung, Vorratshaltung und des Bestellverhaltens unsere Komplexität in der Materialversorgung gemeinsam reduzieren. Damit sparen wir zusammen schon rund 20 %.
Wie geht es dann weiter?
Im zweiten Schritt namens „Integrate“ blicken wir noch tiefer in die Supply Chain zum Kunden. Hier erreichen wir Einsparungen zwischen 50.000 und 2 Mio. €. Wir sehen zum Beispiel, wie der Kunde unsere Produkte verarbeitet und können mit unserem Wissen seine Prozesse optimieren. Ebenso vermeiden wir Dopplungen, etwa bei der Qualitätskontrolle. Wenn wir uns auf gemeinsame Prüfpläne und -methoden einigen, kann sich der Kunde einen Teil seiner umfangreichen Kontrolle im Wareneingang sparen, da wir diese Untersuchungen sowieso im Ausgang vornehmen. Ebenso können wir Transporte zum Kunden zusammenlegen und damit die Kosten verringern. Der dritte Schritt – „Collaborate“ – ist ein tieferer Einblick in die Produktentwicklung des Kunden. Wenn wir etwa wissen, dass er in naher Zukunft ein bestimmtes neues Produkt von uns benötigt, das einen seltenen Rohstoff enthält, können wir das Material vorab bestellen. Viele kleine Maßnahmen ergeben eine Kostenersparnis beim Kunden von bis zu 30 %.
Profitiert davon auch Symrise?
Wenn ein Kunde optimiert bestellt, wird unser Prozess schlanker und damit kosteneffizienter. Ebenso können wir unsere Produktion besser steuern, sobald wir genaue Planzahlen haben. Wir haben auch Vorteile, weil unsere eigenen Lieferanten unsere Erwartungen besser verstehen und mithelfen, unsere Produkte zu verbessern. Das hat sich in den 50 umfangreichen Projekten, die wir schon hinter uns haben, immer bewahrheitet.
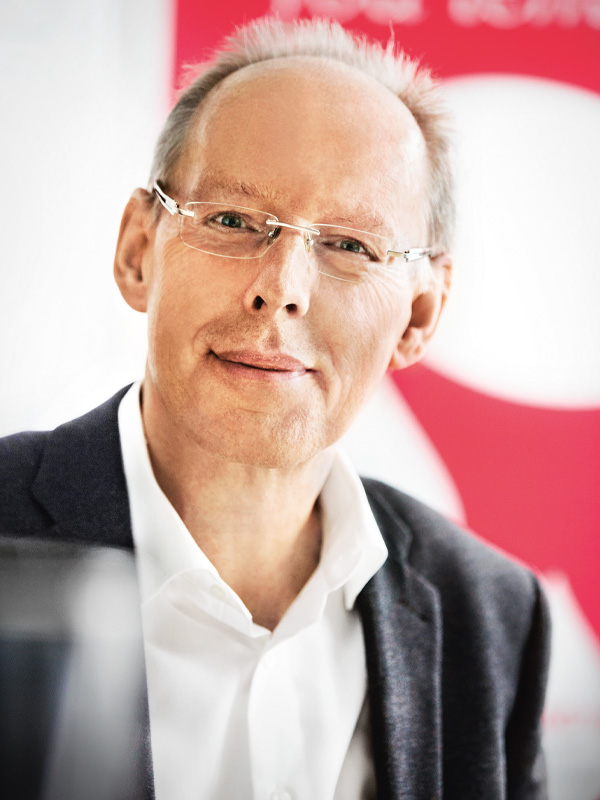
Bernd Körtner leitet bei Symrise im Bereich Operations Flavors die Effizienzsteigerungsprogramme. Eines davon ist „Symchronize™“, das auf eine enge Vernetzung der firmenübergreifenden Supply Chain setzt.
-3 bis -7%
Die Prozesskosten können pro Kunde zwischen 50.000 und 2 Mio. € sinken.