Die Evolution der Menthol-Synthese in Bushy Park
Seit der erfolgreichen Synthese von Menthol vor 50 Jahren und der anschließenden Entwicklung zu einem der größten Lieferanten dieser neuen Substanz hat Symrise seine Prozesse immer wieder optimiert und erneuert. Das Werk in Bushy Park, South Carolina, USA, ist ein hervorragendes Beispiel für die kontinuierlichen Bemühungen von Symrise, sich zu verbessern.
In den ruhigen Weiten von Bushy Park hat sich im Laufe der Jahrzehnte eine Revolution in der Synthese von L-Menthol entwickelt. Die 1977 gegründete Anlage im US-Bundesstaat South Carolina ist führend in der chemischen Verfahrenstechnik und passt sich seitdem dem technologischen Fortschritt und den Anforderungen des Marktes an. Dr. Peter Esser, VP Global Chemical Production und Jared Klein, ASST VP Chemical Production US, seit vielen Jahren Ingenieur und Manager der Bushy Park Menthol Production diskutieren den Werdegang des Werks von seiner Gründung bis heute.
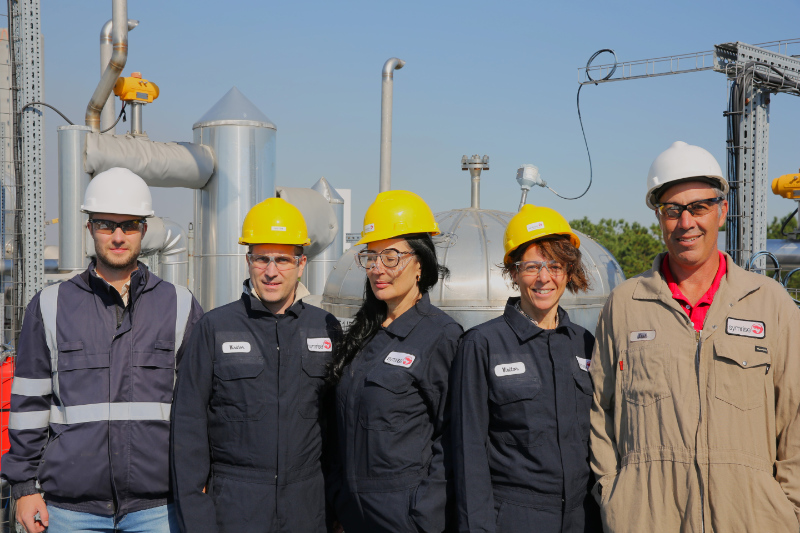
Herr Klein, könnten Sie uns zunächst von den frühen Tagen der Menthol-Werks in Bushy Park erzählen?
Jared Klein: Sicher. Als die Anlage 1976 gebaut wurde, war sie mit einer gewissen Kapazität ausgelegt, die für etwa zwei Jahrzehnte weitgehend unverändert blieb. In dieser Zeit konzentrierten wir uns auf kleine Projekte, um Bottlenecks bei bestehenden Prozesse zu beseitigen, und diese zu optimieren, ohne den Kern der Anlage erheblich zu verändern.
Was waren einige der wichtigsten Veränderungen, die nach diesen ersten zwei Jahrzehnten eingetreten sind?
JK: In den späten 90er und frühen 2000er Jahren begannen wir aufgrund der steigenden Nachfrage einen Expansionsbedarf zu sehen. Die erste große Erweiterung war die Erhöhung unserer D/L-Menthol-Kapazität. Dazu wurden neue Destillationsanlagen und Kristallisatoren installiert, die auch unseren L-Menthol-Ertrag deutlich erhöhten.
Dr. Peter Esser: Darüber hinaus haben wir auch unsere Isomerisierungs- und Racemisierungsprozesse überarbeitet. Diese Bereiche waren immer Teil der Anlage, aber in den letzten zwanzig Jahren haben wir ihre Kapazität und Effizienz durch technologische Upgrades und neue Installationen deutlich erhöht.
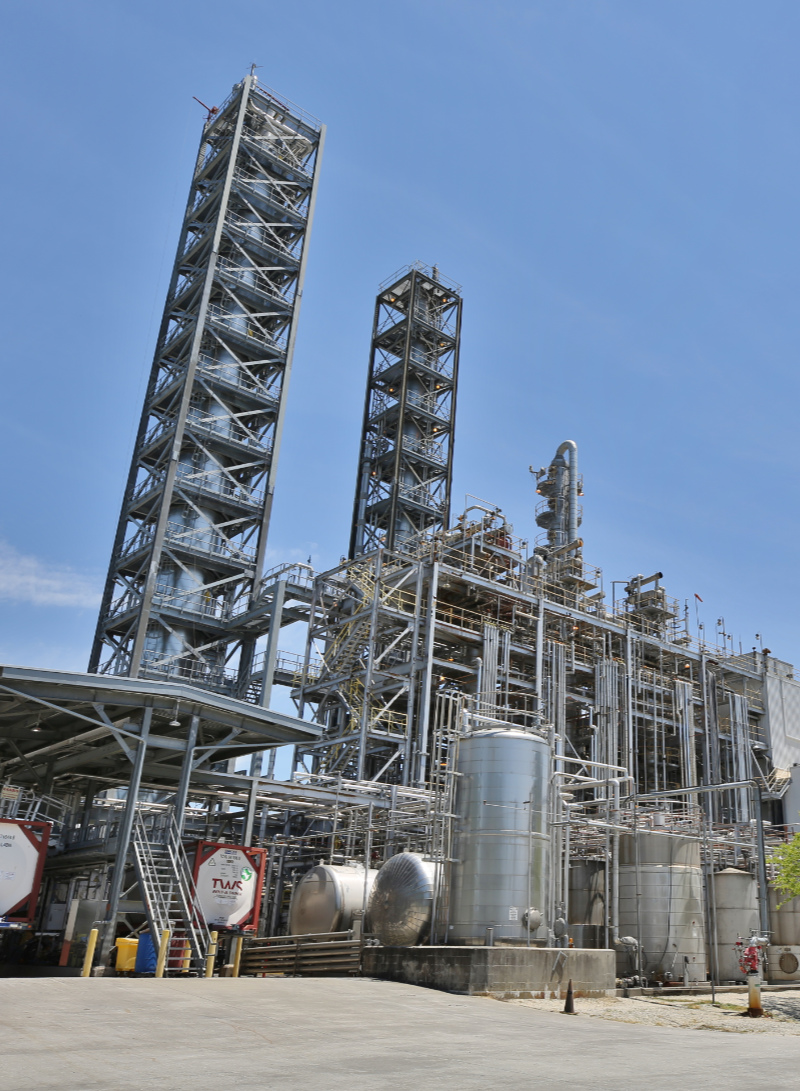
Wie ist die Anlage in Bushy Park im Vergleich zu der in Holzminden?
JK: Ein einzigartiger Aspekt des Standorts Bushy Parks ist, dass wir dort in der Lage sind, den Menthol-Zyklus zu vervollständigen. Wir können D-Menthol, bezogen aus Holzminden und/oder Crude/Isomers von unserem Geschäftspartner, wieder in verwertbares D/L oder L-Menthol umwandeln. Diese Fähigkeit ermöglicht es uns, hocheffiziente und nachhaltige Menthol-Isomere in unseren eigenen Prozessen zu recyceln und wiederzuverwenden.
Können Sie die technologischen Fortschritte und Innovationen, die in die Anlage integriert wurden, näher erläutern?
JK: Im Laufe der Jahre haben wir von Batch-Operationen zu kontinuierlicheren Prozessen gewechselt. Diese Änderung hat nicht nur Energie gespart, sondern auch die Konsistenz unseres Produkts verbessert. Wir haben auch hochmoderne Steuerungssysteme implementiert, die präzisere Operationen ermöglichen, die bei der kontinuierlichen Verarbeitung unerlässlich sind.
Der Markt für Menthol hat sich weiterentwickelt. Wie hat sich Bushy Park an diese Veränderungen angepasst?
JK: Der Menthol-Markt hat sich in der Tat deutlich verschoben. Anfangs konkurrierten wir vor allem mit natürlichen Menthol Quellen, die aufgrund der landwirtschaftlichen Bedingungen einer gewissen Variabilität unterliegen. Da die Produktion von synthetischem Menthol weltweit zugenommen hat, haben wir jedoch eine Verschiebung festgestellt. Die Wettbewerbsdynamik hat sich in der Tat deutlich verändert. Anfangs arbeiteten unsere Hauptkonkurrenten mit einem geringeren Volumen und verwendeten teurere Prozesse. In den letzten 15 bis 20 Jahren sind jedoch große Player auf den Markt gekommen, die ihre Produktionskapazitäten auf ein mit uns vergleichbares Niveau gesteigert haben. Diese Verschiebung hat uns dazu veranlasst, uns nicht nur auf die Steigerung unserer Produktionseffizienz zu konzentrieren, sondern auch auf die Verbesserung der Reinheit und Konsistenz unseres Produkts. Durch den Einsatz fortschrittlicher Technologien und die Optimierung unserer Prozesse haben wir uns einen Wettbewerbsvorteil verschafft, der sicherstellt, dass wir weiterhin die sich wandelnden Anforderungen unserer Kunden erfüllen und am Markt führend bleiben.
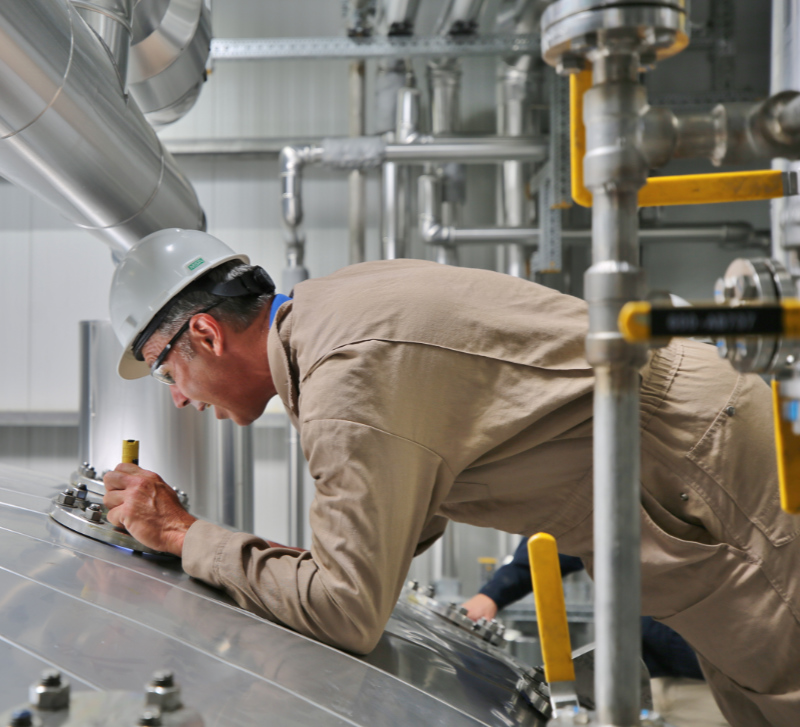
Wie sieht es mit der Nachhaltigkeit aus? Wie hat sich Bushy Park diesem kritischen Thema angenommen?
PE: Nachhaltigkeit steht im Mittelpunkt unserer Aktivitäten. Eines unserer Hauptprojekte war die Installation einer Absorptionskälteanlage, die die Abwärme der Destillation nutzt, um Kühlung für den Menthol-Prozess zu erzeugen. Dies verbessert unsere Energieeffizienz und reduziert aktiv unseren CO2-Fußabdruck für eine nachhaltigere Zukunft
JK: Und in Bezug auf die Produktion haben wir ein lösungsmittelfreies System zur Herstellung von Menthol-Pellets entwickelt, das unsere Umweltauswirkungen im Vergleich zu herkömmlichen Methoden erheblich reduziert.
PE: Im Laufe der Jahre haben wir auch erhebliche Fortschritte bei der Reduzierung unseres Süßwasserverbrauchs gemacht. Der Übergang zur Verwendung von Vakuumtechnologien in unseren neuen Anlagen war entscheidend. Diese Technologien ermöglichen es uns, ohne große Mengen an Süßwasser zu arbeiten, was traditionell für die Kühlung und andere Prozesse notwendig war. Dies schont nicht nur das Wasser, sondern minimiert auch unsere Abwasserproduktion und entspricht unseren Zielen für ökologische Nachhaltigkeit.
Was sind die nächsten Schritte für Bushy Park oder die L-Menthol Produktion von Symrisea im Allgemeinen?
PE: Wir suchen kontinuierlich nach Möglichkeiten, unsere Effizienz und Nachhaltigkeit zu verbessern. Dazu gehört auch die mögliche Übernahme der Bushy-Park-Prozesse in unserem Werk in Holzminden, um unsere Produktionskapazitäten zu vereinheitlichen und den Energieverbrauch weiter zu senken. Durch die Rationalisierung unserer Betriebsabläufe wollen wir unsere Umweltauswirkungen minimieren und zu einer nachhaltigeren Zukunft der Branche beitragen.
JK: Darüber hinaus forschen und entwickeln wir aktiv an Methoden zur Verbesserung unserer Trenntechniken mit dem Ziel, die Menge des Materials zu minimieren, das wir aus unserem System spülen müssen, während wir gleichzeitig ein Produkt von höchster Qualität herstellen.